La nichelatura chimica è un processo che permette di creare rivestimenti compositi a base di nichel e particelle funzionali. Il processo permette di incorporare le particelle nello strato di nichel chimico, a condizione che alcuni parametri vengano rispettati per consentire la co-deposizione delle particelle stesse.
In questo articolo si descrivono le particelle che, quando vengono incorporate in un rivestimento, contribuiscono a ridurre il coefficiente di frizione e a conferire proprietà di anti-aderenza.
Cenni storici
Fin dai primi anni di sviluppo della nichelatura chimica come processo industriale, sono stati individuati metodi per co-deporre particelle autolubrificanti, come il PTFE (Politetrafluoroetilene).
Inoltre, sono state sperimentalmente incorporate nel nichel chimico anche altre particelle che aiutano a ridurre il coefficiente di frizione, come il Disolfuro di molibdeno (MoS2), la Grafite (C) e il Nitruro di boro esagonale (hBN). Queste molecole hanno una struttura cristallina esagonale piatta che consente ai cristalli di scorrere l’uno accanto all’altro su piani paralleli con un attrito minimo. Per esercitare il loro potere antiattrito, è necessario che più piani cristallini scorrano l’uno sull’altro. Le particelle cristalline a struttura lamellare hanno tutte un coefficiente di frizione molto basso e simile tra loro, ma ognuna ha una propria temperatura massima di utilizzo. In questo senso, il prodotto più performante risulta essere il hBN, che è in grado di resistere anche alle alte temperature.
L’incorporazione di queste micro e nano polveri nello strato di nichel chimico è tecnicamente fattibile, tuttavia il processo è stato utilizzato solo in alcune nicchie specifiche a causa dei problemi tecnici legati all’agglomerazione e coagulazione delle particelle. Inoltre, per ottenere un’efficace riduzione della frizione, è necessario incorporare grandi quantità di particelle in modo che, durante lo scorrimento, si formi una quantità sufficiente di lamelle sulla superficie in grado di creare più piani di scorrimento all’interfaccia.
Stato dell’arte
Il PTFE è la molecola più comunemente utilizzata per ridurre l’attrito e appartiene alla famiglia dei polimeri fluorurati, che presentano caratteristiche comuni di basso coefficiente di attrito e antiaderenza. In particolare, il polimero PTFE ha un’elevata temperatura di utilizzo in continuo di 250°C e una temperatura di iniziale degradazione superiore ai 300°C. Il PTFE può essere facilmente utilizzato in soluzione acquosa nei bagni di nichelatura chimica, con particelle depositate di circa 300nm (0,3 µm) di dimensione. A seconda della formulazione dell’elettrolita, le particelle di PTFE vengono co-deposte in quantità variabili, fornendo variazioni del coefficiente di attrito proporzionali alla quantità di PTFE disponibile. Il PTFE, a causa della sua struttura plastica, viene distribuito sulla superficie in seguito allo scorrimento della controparte, creando così un sottilissimo strato di lubrificante solido all’interfaccia tra i due metalli.
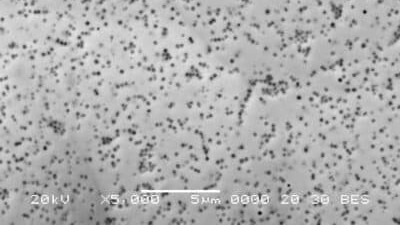
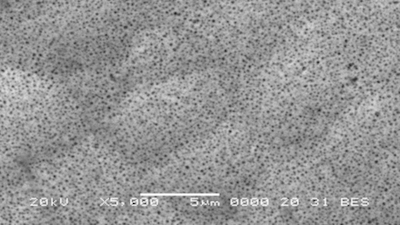
Il coefficiente di attrito del nichel chimico su una superficie metallica, in condizioni di scorrimento a secco, è di circa 0,4-0,5. Tuttavia, se lo strato di nichel chimico contiene una buona quantità di PTFE (almeno il 20-25% in volume), il coefficiente di attrito scende a circa 0,1-0,12, molto vicino al coefficiente di attrito del PTFE puro, pari a 0,05. Il Niplate® 500 PTFE contiene una elevata percentuale di PTFE (25-35%) e presenta un coefficiente di attrito di 0,1 contro acciaio e di 0,08 per lo scorrimento su se stesso. Questo rivestimento è indicato per l’utilizzo in condizioni di scorrimento su superfici a bassa rugosità, con basse forze di contatto e dove non si verifica un’usura particolarmente abrasiva. In applicazioni in cui è presente un’elevata usura abrasiva, i rivestimenti di nichel chimico contenenti particelle ceramiche dure come il Niplate® 600 SiC sono particolarmente efficaci.
Il PTFE ha anche un’elevata capacità di distacco dovuta alla sua inerzia chimica, che non crea legami con i materiali con cui viene a contatto. Sebbene questa caratteristica sia molto utile come distaccante, l’aderenza di uno strato di PTFE puro applicato come rivestimento è scarsa. Un esempio evidente è il rivestimento delle pentole antiaderenti, che tende a staccarsi facilmente dall’alluminio, nonostante una adeguata sabbiatura e preparazione. Tuttavia, l’inserimento del PTFE in una matrice di nichel chimico, molto uniforme e altamente aderente al metallo di base, evita il problema della scarsa aderenza del PTFE e permette di sfruttarne le proprietà anche su particolari con geometria complessa e tolleranze dimensionali strette.
Il Niplate® 500 PTFE , a causa del suo alto contenuto di PTFE, viene preferito ad altri rivestimenti di nichel PTFE commerciali che contengono una quantità inferiore di particelle di PTFE. Ad esempio, viene utilizzato su estrusori per materie plastiche per ridurre le pressioni necessarie all’estrusione. In genere, durante l’estrusione a causa dell’attrito generato dalla forte pressione, si possono verificare bruciature del polimero nella camera di estrusione. Tuttavia, la capacità di scorrimento del rivestimento di nichel PTFE consente di ridurre la pressione di estrusione e di conseguenza l’attrito, eliminando questo problema. Il Niplate® 500 PTFE viene anche utilizzato su piastre di saldatura per film per imballaggio, su parti di macchine per incollaggio ed etichettatura e per evitare accumuli di calcare su ugelli di elettrovalvole per acqua e accumuli di melme e biofilm su scambiatori di calore. È particolarmente utile per l’utilizzo su guide senza lubrificazione, dove può sopportare alte velocità di scorrimento a secco.