Clean energy has become a top priority for governments and industries around the world, as reducing greenhouse gas emissions has become critical to limiting the impact of climate change. In this context, hydrogen is emerging as a promising clean energy source for vehicles and beyond.
Hydrogen vehicles offer significant advantages over electric vehicles, especially for applications that require carrying heavy loads over long distances. Thanks to their greater range and rapid refuelling capacity, these vehicles are particularly suitable for long-distance road haulage of goods, where battery range limitations and long charging times represent significant obstacles.
This feature, combined with the ability to produce hydrogen with renewable energy locally, makes hydrogen vehicles an eco-friendly choice, particularly effective in reducing greenhouse gas emissions compared to fossil fuel vehicles, contributing significantly to reducing the environmental impact in the transportation sector.
In summary, hydrogen is emerging as a promising clean energy source for vehicles. With the right supporting infrastructure, hydrogen could represent an important solution to ensure the green transition in the automotive, heavy and industrial vehicle sectors.
The need to protect mechanical parts from corrosion and wear
Protecting hydrogen circuit components is critical to ensuring the safety and reliability of hydrogen vehicles. The mechanical components of the hydrogen circuit must resist corrosion and wear resulting from the chemical aggression of water and chemicals on the road, such as salts, hydrocarbons and other environmental pollutants.
Importantly, high hydrogen pressures can also cause leakage problems if the sealing surfaces of hydrogen circuit components corrode over time. Corrosion can weaken sealing surfaces and cause hydrogen leakage, which can be dangerous as hydrogen is highly flammable and any leakage could create an explosive environment. For this reason, the safety of hydrogen vehicles also depends on the ability of hydrogen circuit components to resist corrosion and wear over the life of the vehicle.
Using surface treatments can increase the resistance of hydrogen circuit components to mechanical stress and corrosion, prolonging their useful life and ensuring reliable and safe operation of hydrogen vehicles.
The solution: chemical nickel plating and anodizing as protective surface treatments
Chemical nickel plating and anodizing are two surface treatments that can be used to protect hydrogen circuit components from corrosion and wear.
Chemical nickel plating is a process of chemical deposition of a layer of nickel and phosphorus alloy on the surface of the material to be protected. This nickel layer offers corrosion and wear protection, resisting corrosion in both acidic and alkaline environments. In addition, chemical nickel plating can be used to protect all major metal alloys, including **iron, copper and aluminum alloys,**from corrosion.
Anodizing, on the other hand, is an electrochemical process that is used to protect aluminum alloys from corrosion and wear. During anodizing, a layer of aluminum oxide is created on the surface of the aluminum. This aluminum oxide layer acts as a protective barrier against corrosion and wear and can be colored for aesthetic purposes.
The following table summarizes the main characteristics of the coatings.
Features | Chemical nickel plating | Anodization |
---|---|---|
Metals that can be coated | Aluminum Alloys Copper Alloys Iron Alloys | aluminium alloys |
Corrosion resistance in environments with neutral pH | ★★★★☆ on Aluminum alloys ★★★★★ on Copper alloys ★★★★☆ on Iron alloys | ★★★★★ on aluminium alloys |
Corrosion resistance in environments with slightly acidic pH | ★★★☆☆ on Aluminum alloys ★★★★☆ on Copper alloys ★★★☆☆ on Iron alloys | ★★☆☆☆ on aluminium alloys |
Corrosion resistance in environments with slightly alkaline pH | ★★★☆☆ on Aluminum alloys ★★★★★ on Copper alloys ★★★★☆ on Iron alloys | ★★☆☆☆ on aluminium alloys |
Wear resistance | ★★★☆☆ on Aluminum alloys ★★★★☆ on Copper alloys ★★★★☆ on Iron alloys | ★★★★★ on aluminium alloys |
Hydrogen circuit components that can benefit from chemical nickel plating and anodizing
Bipolar plates of the electrolyzer stacks for the production ofH2
Bipolar plates are essential components of electrolyzers since the oxidation-reduction reaction induced by direct current takes place on their surface, transforming water into gaseous H2 and O2. These surfaces must be conductive and must resist the corrosion of alkaline or acidic aqueous solutions necessary for the production ofH2 and O2gases.
On these components, chemical nickel platingcan offer technically advantageous and economically valid solutions for corrosion protection and maintenance of conductivity for some types of electrolyzers (PEM, AEM, AEMWE) where the bipolar plates are made of carbon steel, stainless steel or titanium.
The alternative to chemical nickel plating is precious metal coatings such as gold or platinum or gas phase coatings such as PVD or CVD that have much higher or even exorbitant costs.
Chemical nickel plating has excellent corrosion resistance, and can protect bipolar plates from dissolution and oxidation reactions that occur on the cathode and anode of the stack or electrolytic cell.
Our expertise in the application of chemical nickel plating on bipolar plates, combined with our ability to treat large volumes efficiently, puts us at the forefront as a partner for the scale production of hydrogen electrolyzers, especially now that demand is accelerating.
Micron has developed and manufactures chemical nickel plating formulations in-house and has perfected the technical expertise necessary to ensure effective chemical nickel plating on different types of stainless steel and titanium.
For more information on our chemical nickel plating services and to find out how we can support your hydrogen production electrolyzer project, please do not hesitate to contact us. Visit our website or contact us directly for advice or to request a quote.
Mechanical components of theH2 storage and transfer system in vehicles
Electric vehicle hydrogen circuit components - including valve bodies, reducers, and cylinder parts – often need to be protected from corrosion. Chemical nickel plating and anodizing can protect these components from corrosion and wear, prolonging their life and resistance.
Valve bodies and reducers, used to control the flow of hydrogen in the circuit and to lower the hydrogen pressure from the tank to the operating pressure of vehicle components, can be subject to corrosion and wear due to mechanical friction and exposure to atmospheric and other aggressive agents. Chemical nickel plating and anodizing can protect valve bodies from corrosion and wear, increasing their resistance and prolonging their life.
Metal parts of cylinders, on the other hand, can be subject to corrosion and wear due to their exposure to hydrogen and other chemicals. Chemical nickel plating and anodizing can protect these parts while maintaining their structural integrity and ensuring the safety of the hydrogen circuit.
Micron, specialized in chemical nickel plating, and Durox, expert in anodizing, have extensive experience in coating these components for the hydrogen and automotive sectors. We can offer advanced and complementary solutions for the surface treatment of these components.
Conclusions: the importance of surface protection
In conclusion, protecting hydrogen circuit components through chemical nickel plating or anodizing is an opportunity to ensure the safety and durability of hydrogen vehicles. Corrosion and wear of mechanical components can cause hydrogen leakage and potentially create dangerous situations. Chemical nickel plating and anodizing can improve its life over time ensuring greater safety of the production chain and use of hydrogen as a clean energy source.
Hydrogen represents an important solution for the transition to a sustainable future and protecting components related to its production and use is a fundamental aspect to ensure the safety and effectiveness of hydrogen vehicles in this scenario.
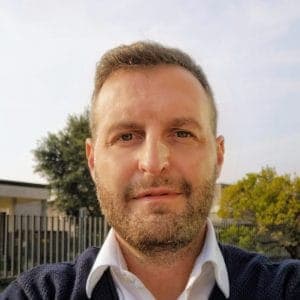