Electroless nickel plating is often applied to mechanical parts for its corrosion resistance properties.
The electroless nickel layer has high chemical resistance and uniform thickness. These characteristics make it possible to create a barrier between the base alloy and the external environment, greatly increasing the corrosion resistance of the part.
This corrosion protection mechanism is completely different from that offered by other coatings, such as zinc plating of steel. In the case of zinc plating, in fact, the zinc layer on the surface is sacrificial to the base metal. The zinc layer has no chemical resistance, but rather corrodes earlier than the base steel. But it is precisely this characteristic, of being sacrificial compared to steel, that allows the base to be protected from corrosion.
Electroless nickel plating protects against corrosion by creating a barrier to the external environment. The possible corrosion trigger points are those areas where the coating is not continuous.
The continuity and integrity of the coating, and thus the degree of corrosion protection, depend on those factors that can compromise the continuity of the layer. Those that most affect the result are mainly attributable to the processing carried out prior to electroless nickel plating.
The main factors are as follows:
- Coating
- Type of electroless nickel (medium, high phosphorus)
- Coating thickness
- Particle to be coated
- Metal alloy of the part
- Production technology (casting, molding, machining, …)
- Workpiece geometry (presence of edges, threads)
- Surface finish and roughness (turned, milled, ground, rough, tumbled, shot-blasted, …)
Coating
Type of electroless nickel
The type of electroless nickel plating, medium phosphorus or high phosphorus electroless nickel, influences corrosion resistance. High-phosphorus electroless nickel plating, in fact, exhibits greater layer uniformity and continuity for the same thickness.
Therefore, parts coated with Niplate 500 high phosphorus electroless nickel will generally have better corrosion behavior than parts with Niplate 600 medium phosphorus electroless nickel.
Coating thickness
Coating thickness also influences corrosion resistance. This is because the greater the coating thickness, the greater the coverage, continuity and uniformity of the coating.
The thickness chosen depends very much on the application, the type of electroless nickel and the base material of the part. In general, where high corrosion resistance is required, the coating thickness should be greater than 20µm in the case of iron or aluminum alloy parts. For copper alloy parts, a thickness of 10µm is sufficient.
Part to be coated
Metal alloy of workpiece
Corrosion behavior is highly dependent on the coated metal alloy. This is because a galvanic couple is created between the two metals at the interface between the base metal and the coating, and this can create accelerated corrosion phenomena:
- Alloys of copper coated with electroless nickel have the best corrosion resistance. These alloys have a reduction potential similar to that of the coating, and thus no galvanic couple is created at the interface. Coated copper alloys can easily exceed 720 hours of salt spray without corrosion, even at low coating thicknesses (around 10µm).
- Iron and aluminium alloys, on the other hand, have a lower reduction potential than the coating. This creates a galvanic couple that accelerates corrosion at the interface. In this case, in order to have good corrosion resistance, it is necessary to increase the treatment thickness (usually greater than 20µm). Increasing the thickness improves the continuity of the layer and thus prevents corrosion initiation, thus eliminating the problem of galvanic couple between base and coating.
Production technology
The best corrosion resistance performance is achieved for parts produced by machining. This is because machining, unlike casting, provides a surface with a better finish, lower roughness and absence of porosity.
Parts produced by casting, be it aluminum or cast iron, have on the surface porosity, inclusions or other defects that compromise the continuity of the layer and thus allow corrosion initiation.
Workpiece geometry
The geometry of the workpiece can also influence corrosion resistance. In fact, the presence of sharp edges or threads can affect the continuity of the coating in those areas and thus create corrosion initiation zones. To improve corrosion performance, it is therefore a good idea to round the edges of the part where possible.
Surface Finish and Roughness
The type of machining used to obtain the surface and its roughness significantly influence corrosion resistance (especially on iron and aluminum alloys).
In fact, where the surface roughness is high (> 1.00 Ra) or the material exhibits tears, burrs or dents, it is easy for corrosion pitting to occur. This is due to the fact that in those areas the coating cannot cover the surface continuously.
Conclusion
The factors influencing corrosion resistance are many, and it is difficult to summarize them because they are interconnected. The choice of treatment specification also depends very much on the application of the part.
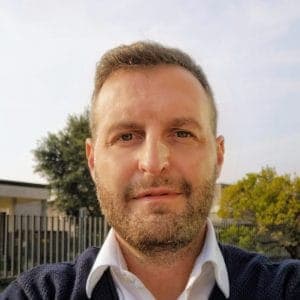