One of the main properties of electroless nickel plating is its corrosion resistance. Electroless nickel plating is in fact used on mechanical metal parts (steel, aluminium alloys or copper) when protection from oxidation and corrosion by external agents is required.
It is used, for example, to protect parts of industrial machinery (packaging machines, machine tools, textile machines), various mechanical devices (pneumatic valves, actuators, fittings) and in the automotive sector (brake pistons, internal components, gears).
Electroless nickel plating increases corrosion resistance due to the chemical resistance of the deposited nickel layer. The layer consists of a binary nickel-phosphorus alloy Ni-P with phosphorus concentrations ranging from 5 to 13%. This alloy has a high resistance to chemical aggression. It is not attacked by neutral salt solutions and withstands alkaline or slightly acidic environments well. The electroless nickel layer is not attacked by chemicals usually found in atmospheres of indoor or outdoor civil, industrial or roadside environments.
The electroless nickel layer therefore protects against corrosion because it acts as a barrier and insulates the base material from external aggressive agents by preventing, delaying or limiting corrosive attack points. Any point of discontinuity in the layer (defects, porosity, inclusions, cracks) can cause corrosion initiation.
The thickness has an important influence on the presence or absence of these discontinuities. The greater the thickness, the lower the ‘porosity’ of the layer and thus the lower the possible corrosion initiation points.
The influence of the base material on the choice of electroless nickel plating thickness
The choice of the correct electroless nickel plating thickness for corrosion resistance requirements depends on the base material to be protected. Corrosion behaviour varies depending on the base material because electrochemical factors between base and coating come into play.
In addition to the base material and thickness, there are many other factors that influence the corrosion resistance of nickel-plated parts. More information can be found in the article Factors influencing the corrosion resistance of electroless nickel .
Nickel plating thickness on iron alloys
In the case where the base material is an iron alloy, the absence of porosity in the layer is very important. On steels any point of discontinuity in the layer can cause corrosion initiation of the base material in an aggressive environment. In addition, due to the reduction potential difference between nickel and base material, galvanic corrosion can be generated on these materials.
Therefore, in the case of applications in which the nickel-plated part may come into contact with water, moisture or aggressive substances, it is necessary to provide increasing thicknesses depending on the aggressiveness of the environment. The table below shows the recommended thickness values.
Nickel plating thickness on aluminum alloys
A similar argument to iron alloys can be made for aluminum alloys with a minor clarification. The corrosion resistance of electroless nickel plating on aluminum is more critical because it can suffer from an under-skin corrosion phenomenon.
To overcome this problem, we have optimized our process of preparing and activating aluminum alloys. This allows us to give the guarantee of maximum corrosion resistance so much so that we apply electroless nickel plating on safety aluminum parts in the automotive sector (brake pistons) on which a corrosion resistance of 720 hours in salt spray (<5% corroded area) is required.
A specific electroless nickel plating treatment was developed to maximize the corrosion resistance of aluminum alloys, the treatment Niplate eXtreme .
Nickel plating thickness on copper alloys
In the case of copper alloy base material, on the other hand, the presence of porosity has very little influence on the corrosion behaviour of the coated part. This is due to the fact that the base material and the layer have a very similar reduction potential and therefore no galvanic corrosion is created. In addition, copper alloys have a higher corrosion resistance and thus corrosion is more limited in the event of corrosion initiation.
Copper alloy parts with electroless nickel-plating treatment can also be used in the marine environment with low electroless nickel plating thickness (15-20µm).
Recommended nickel-plating thicknesses
The choice of thickness is not always simple and straightforward, also because the applications of nickel plated parts are very varied. Sometimes it is only field testing that allows the correct thickness to be defined.
The following table gives indicative values for electroless nickel-plating thicknesses depending on the operating conditions.
Operating condition | Description | Coating thickness on iron alloys and aluminium | Coating thickness on copper alloys |
---|---|---|---|
1 - Light | Indoor use in warm, dry atmosphere | 8±2 µm | 5±2 µm |
2 - Moderate | Indoor environment where condensation may occur. Indoor industrial environments in dry conditions. | 15±2 µm | 8±2 µm |
3 - Severe | Outdoors with frequent wetting by rain, moisture or water. | 30±3 µm | 15±2 µm |
4 - Extremely Heavy | Outdoor use in maritime and aggressive environmental conditions with frequent wetting by rain, moisture or water containing neutral or slightly alkaline pH salts. | 50±5 µm | 20±2 µm |
For more information or advice on the correct treatment thickness to apply, please do not hesitate to contact us.
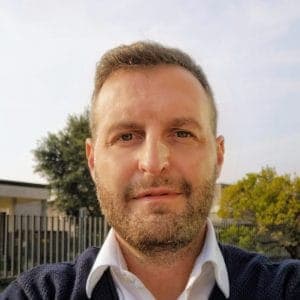