The electroless nickel plating process allows the creation of composite coatings made of functional particles included in a nickel matrix. Through the process, it is possible to incorporate into the chemical nickel layer the particles suspended in the treatment bath.
This article describes the particles that, when incorporated into the coating, cause a reduction in the coefficient of friction and anti-adhesion properties.
Historical background
In the first years of industrial development of chemical nickel plating, a way was found to co-deposit self-lubricating particles such as PTFE (Polytetrafluoroethylene) by dispersing them in the electrolyte for chemical nickel plating.
Other particles, which have the advantage of reducing the coefficient of friction, have also been incorporated experimentally into electroless nickel. These are mainly Molybdenum Disulfide (MoS2), Graphite (C), and Hexagonal Boron Nitride (hBN). These molecules have a flat hexagonal crystalline structure which allows the crystals to slide in parallel planes with very low friction. Several crystalline planes must slide over each other to exert their anti-friction power. The crystalline particles with a lamellar structure all have a very low and comparable coefficient of friction, but each one has its temperature limit for use. In this sense, the best-performing product is hBN which can withstand high temperatures.
The incorporation of these micro and nanopowders in the chemical nickel layer is feasible, but due to plant engineering problems caused by the tendency of the particles to self-agglomerate and coagulate, it is used in niche sectors and has never been developed widely in the industrial field. In addition to the installation problems, there is the need to incorporate particles in large quantities. During sliding, an adequate amount of flakes must be available on the surface, sufficient to produce more sliding planes at the interface, which are effective in lowering friction.
State of the art
PTFE is the most widely used molecule in the field of friction reduction and belongs to the family of fluorinated polymers which share the characteristics of low friction coefficient and non-stick properties. In particular, the PTFE polymer has a high continuous use temperature of 250°C and an initial degradation temperature above 300°C. PTFE has the great advantage of being able to be used in the aqueous dispersion in electroless nickel baths with a deposited particle size of about 300nm (0.3 µm). Depending on the chosen supplier, the PTFE particles can be co-deposited in larger or smaller quantities, providing different coefficients of friction, proportional to the available PTFE in the nickel matrix. The PTFE, having a plastic structure, allows it to be “smeared” by the sliding of the counterpart on the surface, thus creating a very thin film of solid lubricant at the interface of the two metals.
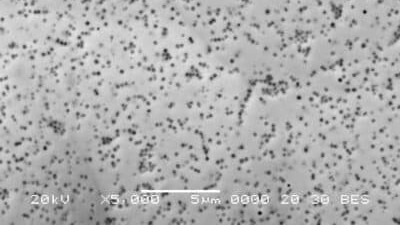
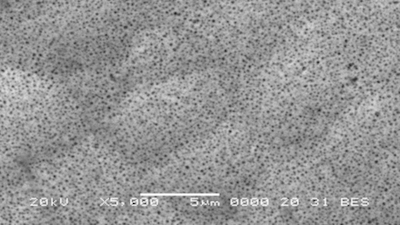
The dry sliding friction coefficient of electroless nickel on a metal counterpart is 0.4-0.5. If the electroless nickel layer contains a good amount of PTFE (at least 20-25% by volume) it lowers its friction coefficient to about 0.1-0.12 which is very close to the CoF of 0.05 of the pure PTFE. Our Niplate® 500 PTFE has a high percentage of PTFE (25-35%) and its friction coefficient is 0.1 against steel and 0.08 for sliding on itself. The coating is suitable for sliding surfaces with low roughness, and low contact forces without particularly abrasive wear. In applications where abrasive wear occurs, electroless nickel coatings containing hard ceramic particles such as Niplate® 600 SiC work well.
Another important feature of PTFE is its chemical inertness, which does not create bonds with the materials it comes into contact with. While on the one hand, it is very useful as a release agent, on the other hand, the adhesion of the pure PTFE layer, applied as a coating, is poor. A significant example is non-stick pans where the coating, unfortunately, peels off very easily from the aluminium despite adequate sandblasting and preparation. The inclusion of PTFE in a Nickel matrix, very uniform in thickness and very adherent to the base metal, avoids the problem of its poor adherence and allows its properties to be used even on internal cavities with high dimensional accuracy.
The high PTFE content of Niplate® 500 PTFE makes it preferable to other coatings of the same type, but which contain fewer particles. Niplate 500®PTFE is used, for example, on extruders for plastics to reduce the pressures required for extrusion. Usually, the friction produced by the high extrusion pressure can cause burns to the polymer to be extruded. These burns are eliminated by the flow capacity of the chamber plated with Niplate 500®PTFE and the applied extrusion pressure will be reduced. This treatment is used on sealing plates for packaging films, glueing and labelling machines. Niplate 500®PTFE is very useful to avoid limescale growth on water solenoid valve nozzles and sludge and biofilm build-up on heat exchangers. A common use is on non-lubricated guides, which can withstand high dry running speeds.