Customers often have questions about how coatings affect part size. Some of the most common questions are: what is the change in size caused by the coating, should tolerated holes be masked, and what happens to threads?
Electroplating coatings add material to the surface of the part. Consequently, the greater the thickness of the coating, the greater the change in dimension. However, it is important to keep in mind that this is only valid if the thickness of the coating is uniform across the entire surface. Excessive variability in thickness, under tight tolerances, could compromise adherence to the final dimensions.
In this context, it is important to make a distinction between electrolytic coatings, such as zinc plating, nickel plating and chrome plating, and electroless nickel plating.
Electrolytic coatings
Electrolytic coatings are applied by the use of electric current and exhibit little uniformity in thickness. This is due to the fact that the current does not distribute evenly over the surface of the workpiece, causing phenomena such as the spike effect (i.e., increased thickness in the sharpest areas of the workpiece and on the edges), poor penetration into holes (with a reduction in thickness to zero at a certain depth), and variations in thickness between workpieces (depending on the position of the workpieces on the treatment frame).
In general, when using electrolytic coatings, it is advisable to provide masking of tolerated or threaded holes, especially if they are deep. In addition, it is important to check that excessive thickness variability does not compromise compliance with tolerances for tolerated outside diameters. For example, parts coated with hard chrome are often machined to match the required tolerances.
Electroless nickel plating
Electroless nickel coating, as opposed to electrolytic coatings, is achieved through a chemical reaction without the use of electric current. This avoids the thickness non-uniformity phenomena described above.
The thickness of electroless nickel is constant over the entire surface of the part, with no distinction between internal or external areas, between edges or flat surfaces. In addition, the thickness of the treatment is equally uniform among the various parts on the same nickel-plating rack.
As for electroless nickel plating, masking and rework are usually unnecessary. It is sufficient to calculate the size of the machining considering that the diametral growth is twice the thickness of the coating.
It is important to make an additional point regarding threads. Due to the geometry of threads, the diametral increment is no longer twice the thickness of the coating, but four times the thickness. It is therefore necessary to take this into account when calculating the machining dimensions.
To aid in the determination of machining dimensions, a pre-treatment dimensional tolerances calculation tool can be used, which can be found on the Pre-treatment Dimensional Tolerances Calculator page.
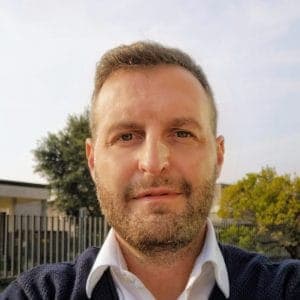