Chemische Vernickelung ist ein Verfahren zur Herstellung von Nickel-basierten Verbundbeschichtungen und funktionellen Partikeln. Das Verfahren ermöglicht die Einbettung der Partikel in die chemische Nickelschicht, sofern bestimmte Parameter eingehalten werden, um die Co-Abscheidung der Partikel zu ermöglichen.
Dieser Artikel beschreibt Partikel, die, wenn sie in eine Beschichtung eingebettet sind, dazu beitragen, den Reibungskoeffizienten zu reduzieren und Antihaft-Eigenschaften zu verleihen.
Geschichtlicher Hintergrund
Seit den ersten Jahren der Entwicklung der chemischen Vernickelung als industrieller Prozess wurden Methoden zur Co-Abscheidung von selbstschmierenden Partikeln wie PTFE (Polytetrafluorethylen) identifiziert.
Darüber hinaus wurden experimentell auch andere Partikel in chemisches Nickel eingearbeitet, die zur Verringerung des Reibungskoeffizienten beitragen, wie Molybdändisulfid (MoS₂), Graphit (C) und hexagonales Bornitrid (hBN). Diese Moleküle haben eine flache hexagonale Kristallstruktur, die es den Kristallen ermöglicht, mit minimaler Reibung nebeneinander auf parallelen Ebenen zu gleiten. Um ihre reibungsmindernde Wirkung auszuüben, müssen mehrere kristalline Ebenen übereinander liegen. Lamellar strukturierte kristalline Partikel haben alle einen sehr niedrigen Reibungskoeffizienten und sind einander ähnlich, aber jedes hat seine eigene maximale Betriebstemperatur. In diesem Sinne ist das leistungsstärkste Produkt das hBN, das auch hohen Temperaturen standhält.
Die Einbettung dieser Mikro- und Nanopulver in die chemische Nickelschicht ist technisch machbar, das Verfahren wurde jedoch aufgrund technischer Probleme im Zusammenhang mit der Agglomeration und Koagulation von Partikeln nur in bestimmten Nischen eingesetzt. Um eine effektive Reduzierung der Reibung zu erreichen, müssen große Mengen an Partikeln eingearbeitet werden, sodass sich während des Gleitens eine ausreichende Anzahl von Lamellen auf der Oberfläche bildet, die in der Lage sind, mehrere Gleitebenen an der Schnittstelle zu erzeugen.
Stand der Technik
PTFE ist das am häufigsten verwendete Molekül zur Reibungsminderung und gehört zur Familie der fluorierten Polymere, die gemeinsame Eigenschaften von niedrigem Reibungskoeffizienten und Antihaftwirkung aufweisen. Insbesondere hat das PTFE-Polymer eine hohe Dauereinsatztemperatur von 250 °C und eine anfängliche Abbautemperatur von über 300 °C. PTFE kann leicht in wässriger Lösung in chemischen Vernickelungsbädern mit abgeschiedenen Partikeln von etwa 300 nm (0,3 µm) Größe verwendet werden. Abhängig von der Elektrolytformulierung werden PTFE-Partikel in unterschiedlichen Mengen mitabgeschieden, wodurch der Reibungskoeffizient proportional zur verfügbaren PTFE-Menge variiert. PTFE wird aufgrund seiner Kunststoffstruktur nach dem Gleiten des Gegenstücks auf der Oberfläche verteilt, wodurch eine sehr dünne Schicht aus festem Schmiermittel an der Schnittstelle zwischen den beiden Metallen entsteht.
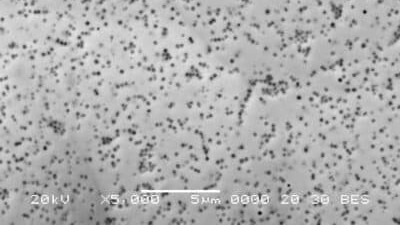
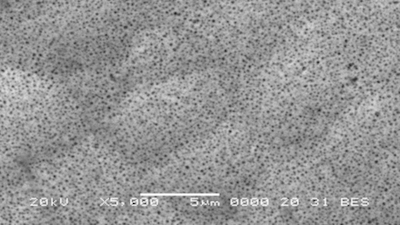
Der Reibungskoeffizient von chemischem Nickel auf einer Metalloberfläche unter Trockenlaufbedingungen beträgt etwa 0,4–0,5. Wenn die chemische Nickelschicht jedoch eine gute Menge PTFE enthält (mindestens 20–25 Volumenprozent), sinkt der Reibungskoeffizient auf etwa 0,1–0,12, was dem Reibungskoeffizienten von reinem PTFE von 0,05 sehr nahekommt. Niplate® 500 PTFE enthält einen hohen Anteil an PTFE (25–35 %) und hat einen Reibungskoeffizienten von 0,1 gegenüber Stahl und 0,08 beim Gleiten gegen sich selbst. Diese Beschichtung ist für den Einsatz unter Gleitbedingungen auf Oberflächen mit geringer Rauheit, geringen Kontaktkräften und ohne besonders abrasiven Verschleiß geeignet. In Anwendungen mit hohem Schleifverschleiß sind chemische Nickelbeschichtungen mit harten Keramikpartikeln wie Niplate® 600 SiC besonders effektiv.
PTFE hat auch eine hohe Trennfähigkeit aufgrund seiner chemischen Trägheit, die keine Bindungen zu den Materialien herstellt, mit denen es in Kontakt kommt. Obwohl diese Eigenschaft als Trennmittel sehr nützlich ist, ist die Haftung einer Schicht aus reinem PTFE, die als Beschichtung aufgetragen wird, schlecht. Ein offensichtliches Beispiel ist die Beschichtung von Antihaft-Kochgeschirr, die dazu neigt, sich trotz geeigneter Sandstrahlung und Vorbereitung leicht von Aluminium zu lösen. Das Einfügen von PTFE in eine chemische Nickelmatrix, die sehr gleichmäßig und sehr haftend auf dem Grundmetall ist, vermeidet jedoch das Problem der schlechten Haftung von PTFE und ermöglicht es, seine Eigenschaften auch auf Teilen mit komplexer Geometrie und engen Maßtoleranzen auszunutzen.
Niplate® 500 PTFE wird aufgrund seines hohen PTFE-Gehalts anderen handelsüblichen PTFE-Nickelbeschichtungen vorgezogen, die weniger PTFE-Partikel enthalten. Zum Beispiel wird es auf Extrudern für Kunststoffe verwendet, um die für die Extrusion erforderlichen Drücke zu reduzieren. Typischerweise kann es während der Extrusion aufgrund der durch den starken Druck erzeugten Reibung zu Verbrennungen des Polymers in der Extrusionskammer kommen. Die Gleitfähigkeit der PTFE-Nickelbeschichtung ermöglicht es jedoch, den Extrusionsdruck und damit die Reibung zu reduzieren, wodurch dieses Problem beseitigt wird. Niplate® 500 PTFE wird auch auf Folienschweißplatten für Verpackungen, auf Teilen von Klebe- und Etikettiermaschinen und zur Vermeidung von Kalkablagerungen auf Düsen von Wassermagnetventilen sowie von Schlamm- und Biofilmablagerungen auf Wärmetauschern eingesetzt. Es ist besonders nützlich für den Einsatz auf nicht geschmierte Führungen, wo es hohen Trockenlaufgeschwindigkeiten standhält.