Anodisieren (auch anodische Oxidation genannt) ist ein elektrochemischer Prozess, der es ermöglicht, auf der Metalloberfläche des behandelten Werkstücks eine kompakte Oxidschicht zu erhalten. Dieser Prozess verwendet elektrischen Strom und sein Name hängt damit zusammen, dass das zu behandelnde Teil mit der Anode einer Elektrolysezelle verbunden ist. Das Anodisieren ist die wichtigste Schutzbehandlung, die auf Aluminium durchgeführt wird. Andere Metalle, die leicht anodisiert werden können, sind Titan und Magnesium.
Anodisieren von Aluminium
Der erste Anodisier-Vorgang, der zwischen 1920 und 1930 entwickelt wurde, basierte auf Chromsäure. Eine solche Beschichtung, die man als Chromsäureanodisierung bezeichnet, wird aufgrund der Karzinogenität von Chromsalzen jetzt nur noch für bestimmte Sektoren wie Militär und Luftfahrt durchgeführt.
Derzeit ist der am weitesten verbreitete und am häufigsten verwendete Anodisier-Vorgang der auf Schwefelsäure basierende.
Die zu behandelnden Stücke werden in eine 20%-ige Schwefelsäurelösung getaucht, die als Elektrolyt wirkt. Auf das Aluminiumteil wird der Pluspol aufgebracht, während der Minuspol mit einer in der Lösung vorhandenen Kathode verbunden wird. Durch die Bestromung der Elektrolysezelle entwickeln sich Sauerstoff-Ionen auf der Oberfläche des zu behandelnden Werkstücks, die in Kombination mit den Aluminiumatomen eine harte und kompakte Schicht aus Aluminiumoxid bilden, mit hervorragenden Eigenschaften wie:
- Korrosionsbeständigkeit
- Verschleißfestigkeit
- Härte
- Gleichmäßigkeit der Dicke
- Möglichkeit der Färbung mit Pigmenten, die in die Oxidschicht eindringen
- dielektrische Isolation
Aufbau der Oxidschicht
Aluminiumoxid, das durch den Anodisier-Vorgang in Schwefelsäure gebildet wird, hat eine Wabensäulenstruktur mit sechseckigen Zellen und einer zentralen Porosität, die sich fast über die gesamte Tiefe erstreckt. Der Prozess des Hartanodisierens bildet Porosität mit einem Durchmesser von etwa 20–40 nm und einem Porenabstand von etwa 100 nm.
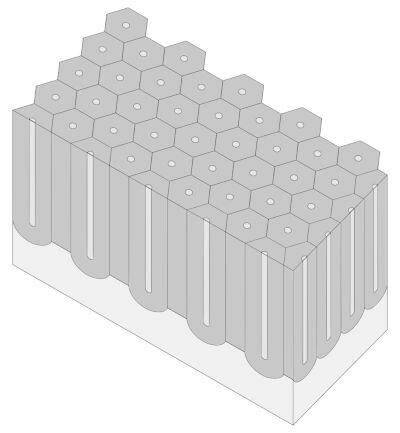

Es gibt zwei Arten des Anodisierens mit unterschiedlichen Oberflächeneigenschaften und Prozessparametern:
Art des Anodisierens | Eigenschaften |
---|---|
Natürliches oder dekoratives Anodisieren OX-A | Wird verwendet, um eine gute Korrosionsbeständigkeit in nicht aggressiven Umgebungen und eine diskrete Beständigkeit gegen Verschleiß und Kratzer zu gewährleisten. Verwendet im dekorativen Bereich, da es in verschiedenen Farben gefärbt werden kann. |
Harteloxieren OX-HS – OX-W | Wird auf feinmechanischen Teilen verwendet, um eine ausgezeichnete Korrosions- und Verschleißfestigkeit, hohe Härte und Festigkeit in aggressiven Umgebungen zu gewährleisten. |
Hartanodisieren des Aluminiums
Mit dem Begriff Harteloxieren wird eine sehr harte und kompakte Aluminiumoxidbeschichtung identifiziert, die dicker ist als das dekorative Anodisieren. Sie wird vor allem in der Feinmechanik auf mechanisch bearbeiteten Werkstücken verwendet, ob aus dem Vollen, extrudiert, gegossen, druckgegossen oder gewalzt, um die Korrosionsbeständigkeit, Härte und Verschleißfestigkeit zu erhöhen.
Technische Referenznormen
Die technischen Normen und internationalen Normen für das Harteloxieren lauten wie folgt:
Norm/Standard | Titel |
---|---|
ISO 10074 | Anodisieren von Aluminium und Aluminiumlegierungen – Spezifikation für harte anodische Oxidationsbeschichtungen auf Aluminium und Aluminiumlegierungen |
MIL-A-8625 | ANODIC COATINGS FOR ALUMINUM & ALUMINUM ALLOYS - Type III: Hard Anodic Coatings |
UNI 7796 | Beschichtungen für die anodische Oxidation von Aluminium und Aluminiumlegierungen – Dicke der anodischen Oxidation – Allgemeine Prüfanforderungen und -anweisungen |
Ästhetisches Aussehen
Das Harteloxieren nimmt die Oberflächenmorphologie des Werkstücks wieder auf und es ist daher möglich, die Oberflächen des Aluminiums auch nach dem Anodisieren beizubehalten (z. B. glänzend, satiniert, gebürstet, gestrahlt, kugelförmig, sandgestrahlt usw.).
Die Beschichtung nimmt eine Selbstfärbung an, die stark von der verwendeten Aluminiumlegierung abhängt und zwischen grau, dunkelgrau und braun variieren kann. Nach der Behandlung kann die Oberfläche mit schwarzem, blauem oder rotem Farbstoff pigmentiert werden. Diese Pigmente dringen in die Eloxalschicht ein und färben sie. Da die Grundfarbe der anodisierten Schicht im Gegensatz zu natürlichen Eloxalbehandlungen dunkel ist, nehmen Harteloxalbehandlungen eine tiefschwarze, dunkelblaue und dunkelrote Färbung an. Die Dicke wirkt sich dadurch aus, dass die Beschichtung dunkler wird, wenn die Dicke zunimmt. Legierungen, die viel Kupfer enthalten, erhalten ein bronzenes Aussehen und Legierungen, die viel Silizium (>12 %) enthalten, können eine ungleichmäßige Färbung aufweisen. Das Harteloxieren, das eine dunkle Farbgebung verleiht, eignet sich für dunkle und deckende Farben und wird in der Regel in schwarz gewählt, sowohl wegen der hervorragenden ästhetischen Leistung als auch zur Vereinheitlichung der Farbe in Gegenwart verschiedener Legierungen.
Anodisierbare Aluminiumlegierungen
Mit einigen kleinen Ausnahmen sind alle Aluminiumlegierungen anodisierbar. Die größten Schwierigkeiten treten bei Legierungen auf, die andere Elemente als Aluminium in großen Mengen enthalten, da nur Aluminium zur Bildung der Oxidschicht beiträgt. Daraus folgt, dass Legierungen, die hohe Kupfermengen enthalten, wie die der Serie 2000, keine hohe Dicke erreichen und die Oxidschicht etwas weniger kompakt und weniger korrosions- und verschleißbeständig ist. Siliziumhaltige Legierungen in Mengen von mehr als 12 % können eine geringere Dicke und Gleichmäßigkeit der Beschichtung aufweisen, was zu einer geringeren Beständigkeit gegen Korrosion, Verschleiß und manchmal zu Farbunebenheiten führt.
Anodisierungsdicke
Ein besonderes Merkmal des Anodisierens ist die Möglichkeit, die Werkstücke mit einer gleichmäßigen und kalibrierten Dicke auf fast allen Oberflächen zu beschichten. Eine Ausnahme können Löcher mit kleinem Durchmesser sein, die sehr tief sind, bei denen die Durchdringungsfähigkeit der Beschichtung individuell beurteilt werden muss.
Die Standarddicke beim Harteloxieren beträgt 30–50 µm, aber je nach Bedarf können kleinere oder größere Dicken gewählt werden. Bei sehr engen Toleranzen neigt man dazu, die Anodisierungsdicke zu verringern und/oder eine engere Toleranz wie z. B. 30±5 µm zu definieren.
Zunahme der Größe
Die Dicke ist nach der Behandlung sowohl auf der Außenseite als auch auf der Innenseite des Aluminiumteils um 50 % größer. Die radiale Abmessungszunahme entspricht somit der Hälfte der Behandlungsdicke.
Korrosionsbeständigkeit
Das Harteloxieren hat aufgrund der größeren Dicke und der höheren Kompaktheit der Oxidschicht eine höhere Korrosionsbeständigkeit als das dekorative Anodisieren. Diese Beständigkeit kann durch die in der Beschichtung vorhandenen Porositäten beeinträchtigt werden, die der erste Korrosionsauslöser sind. Um die Korrosionsbeständigkeit zu erhöhen, wird daher nach dem Anodisieren eine Behandlung durchgeführt, die als Fixierung bezeichnet wird. Es gibt verschiedene Arten von Versiegelungen und die beiden am häufigsten industriell verwendeten und international anerkannten sind:
- Heißversiegelung: Eintauchen in Wasser bei einer Temperatur von etwa 95 °C, was eine Oberflächenfeuchtigkeit der Aluminiumoxidschicht ermöglicht und die Porosität schließt, und damit eine bessere Korrosionsbeständigkeit ermöglicht.
- Kaltversiegelung: Eintauchen in eine Nickelfluoridlösung bei Raumtemperatur. Nickelsalze dringen in die Porosität der Beschichtung ein und verbessern die Korrosionsbeständigkeit.
Die Heißsiegelung ist zwar energieintensiv, da sie bei 95 °C stattfindet, wird jedoch der mit Nickelsalzen zunehmend vorgezogen, die krebserregend sind und Hautallergien hervorrufen können. Im Lebensmittelbereich kann beispielsweise die Versiegelung auf Nickelbasis nicht eingesetzt werden.
Das Anodisieren ist sehr widerstandsfähig gegen Korrosion bei Kontakt mit Alkoholen, Kohlenwasserstoffen und neutralen Lösungen. Saure oder basische Lösungen lösen das Aluminiumoxid auf und vereiteln die Korrosionsschutzbarriere. Die Auflösungsgeschwindigkeit der Eloxalschicht ist proportional zur Säure oder Basizität der Lösung und fällt bei basischer Lösung höher aus.
Harteloxieren OX-W ist eine Behandlung, die speziell entwickelt wurde, um die ohnehin schon hervorragende Korrosionsbeständigkeit des Hartanodisierens zu erhöhen. Auf einigen Legierungen können 1000 Stunden Exposition gegenüber neutralem Salznebel nach ISO 9227 erreicht werden, ohne dass Korrosion auftritt. OX-W eignet sich auch zum Schutz von Legierungen mit hohem Siliziumgehalt, die beim Standard-Anodisieren auf Schwierigkeiten stoßen könnten.
Härte, Dichte und Verschleißfestigkeit
Das Harteloxieren bietet eine hohe Härte, die je nach verwendeter Aluminiumlegierung variiert.
Die Spezifikation ISO 10074 legt die Mindesthärte fest, die bestimmte Legierungen haben müssen. Die Härte wird nach ISO 4516 auf einer Schicht mit einer Dicke zwischen 25–50 µm und einer Belastung von 50 g HV 0.05 gemessen.
Legierung | Vickershärte |
---|---|
Knetlegierung | 400 HV |
2000er Serie | 250 HV |
5000er Serie mit Magnesium >2 % | 300 HV |
7000er Serie | 300 HV |
Schmelzlegierungen mit Kupfer <2 % und/oder Silizium <8 % | 250 HV |
Die Dichte, gemessen nach ISO 2106 auf einer 50 µm ± 5 µm-Beschichtung ohne Versiegelung, muss folgende Mindestwerte aufweisen:
Legierung | Beschichtungsdichte |
---|---|
Knetlegierung | 1100 mg/dm² |
2000er Serie | 950 mg/dm² |
5000er Serie mit Magnesium >2 % | 950 mg/dm² |
7000er Serie | 950 mg/dm² |
Schmelzlegierungen mit Kupfer <2 % und/oder Silizium <8 % | 950 mg/dm² |
Die hohe Härte und Kompaktheit der Oxidschicht und die säulenförmige Struktur führen dazu, dass das Harteloxieren eine hohe Verschleißfestigkeit erreicht, die die der chemischen Vernickelung übertrifft und mit einer dicken Hartverchromung vergleichbar ist. Der Taber Abraser ist ein Test, der den Verschleiß von Gleitbeschichtungen anhand von Schleifrädern bestimmt. Nach ISO 10074 muss der Massenverlust nach 10.000 Zyklen unter folgenden Werten liegen:
Legierung | Max. Gewichtsverlust |
---|---|
Knetlegierung | 15 mg |
2000er Serie | 35 mg |
5000er Serie mit Magnesium >2 % | 25 mg |
7000er Serie | 25 mg |
Schmelzlegierungen mit Kupfer <2 % und/oder Silizium <8 % | - |
Rauheit
Das Harteloxieren trägt dazu bei, die Oberflächenrauheit geringfügig zu erhöhen und ist auf Oberflächen mit geringer Rauheit bei der mechanischen Bearbeitung besser spürbar.
Das Harteloxieren OX-W hat die Eigenschaft, die Erhöhung der Oberflächenrauheit einzudämmen. Durch die Verwendung einiger spezifischer Aluminiumlegierungen und die Festlegung der korrekten Betriebsparameter ist es möglich, die Endrauheit auf Werten unter 0,5 Ra zu halten.
Lebensmittelkontakt
Die Norm „EN 14392 Requirements for anodised products for use in contact with foodstuff“ legt die Anforderungen an Eloxalbehandlungen von Aluminiumteilen fest, die für den Kontakt mit Lebensmitteln bestimmt sind.
Die von Durox srl durchgeführten Behandlungen entsprechen der Norm EN 14392, wenn die folgenden Anforderungen erfüllt sind:
- Die chemische Zusammensetzung der Aluminiumlegierungen der zu anodisierenden Teile muss, soweit anwendbar, den Anforderungen der Normen EN 601 oder EN 602 entsprechen.
- Die Anodisier-Behandlungen müssen der Versiegelungsphase unterzogen werden, die ausdrücklich angefordert werden muss.